A major manufacturer of popular beverages has appointed a local distributor to serve a specific territory. The demand for the beverages has a pronounced seasonal pattern. The distributor performs well overall, but is repeatedly unable to keep up with fulfilling many customer orders during peak demand periods. The distributor's current delivery capability is stretched to deliver 60 tons of merchandise per day whereas the season's peak demand periods need a daily delivery capability of up to 100 tons.
The distributor is under pressure to fully meet the year-round market demand in order to stay in business. The distributor's management wants to identify and consider more cost-effective options as resorting to adding more trucks and drivers would not be economically feasible.
A business analyst (BA) has spent several days observing and measuring the warehouse activities to understand the situation and to gain insights into possible solutions. The delivery workflow is a four-step process: (1) picking the orders and assembling them on trays, (2) bringing the trays to the loading bay, (3) loading the orders into trucks, and (4) delivering the orders to customers. As the following table illustrates, overall performance depends is dependent on five major resources: (1) the workers who pick the orders and load them into trucks, (2) the tallyers who check the orders, (3) the drivers, (4) the trucks, and (5) eight loading bays (LBs).
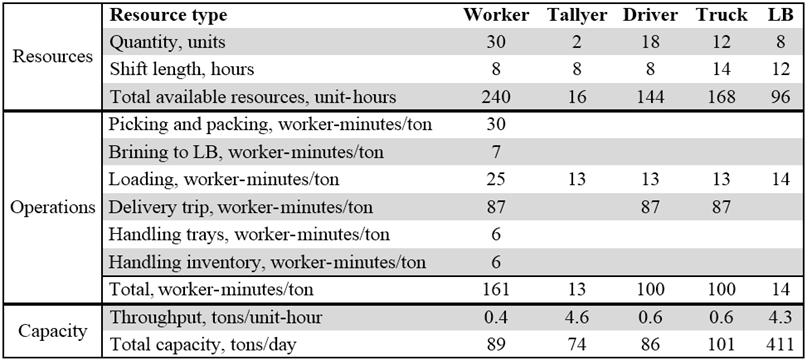
Each truck can only make two trips a day. The BA has noticed that only 30% of trips have their orders available for loading when a truck arrives. Otherwise the truck has to wait one extra hour until the orders are picked and brought to the loading bay.
If trucks are the only constraint, approximately how many hours are lost due to this downtime?